Designing an Adjustable Conveyor System For a Multi-sized Bottling System
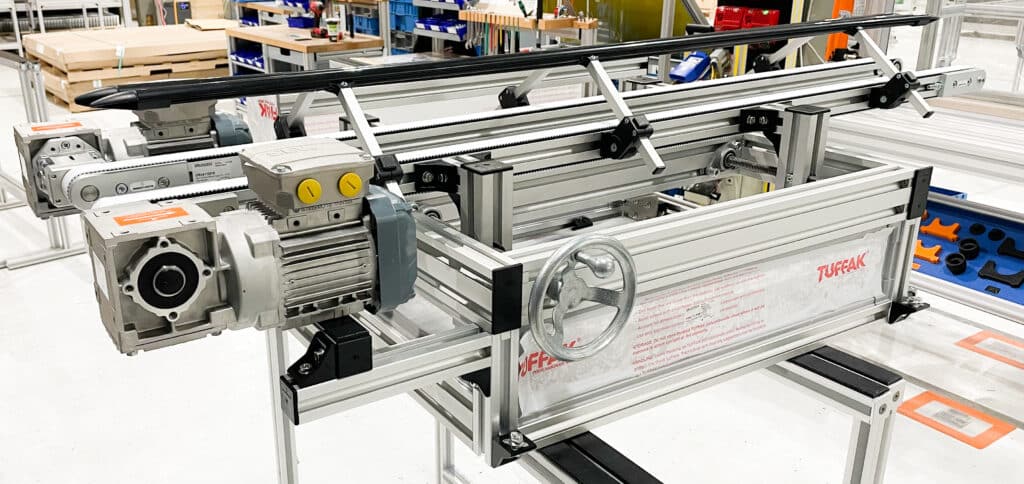
To make a single conveyor system that can handle multiple-size products, it must be designed with adjustability in mind. For example, one Robotunits customer recently installed an automated conveyor system to produce bottled water. The packaging and assembly specialist wanted to smoothly transfer bottles from one conveyor system to another before filling. However, the transfer portion of the production line had to handle bottles of various widths and heights, requiring custom conveyors that could be adjusted in both the X, Y and Z axes. The system also had to incorporate the customer’s assemblies, alongside our modular products for automated systems.
Here’s what the setup looked like:
A preexistent customer-supplied component moves bottles to a section with two sets of 32-millimeter-wide Robotunits C8T Timing Belts Conveyors. Each pair of timing belts is situated upright to create a dual-lane that pushes the bottles. These bottomless “hugger” conveyors allow machine vision components to inspect the bottles for quality. The imperfect bottles are pushed aside, and the good bottles go to a Robotunits Linear Motion Unit, which transfers them to the end-customer’s existing conveyor system.
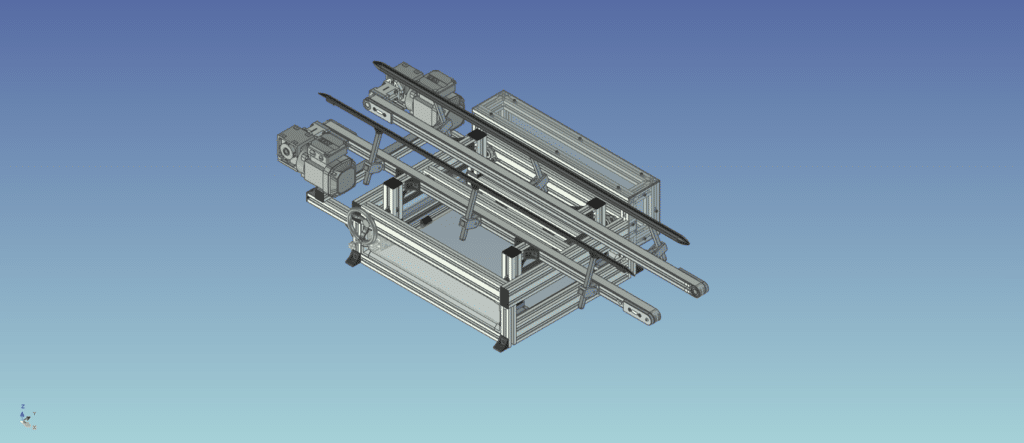
The Linear Motion Unit features a simple, modular design, is highly customizable and — thanks to its high wear resistance — achieves smooth and quiet operation
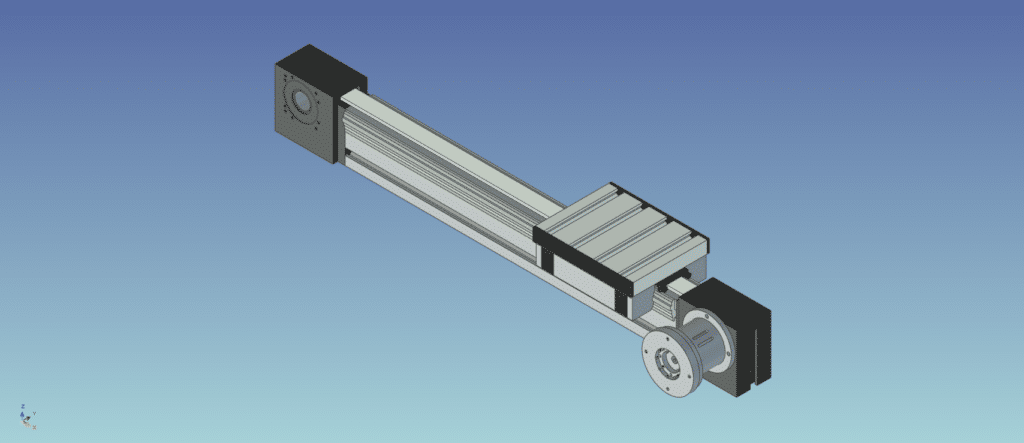
Our Timing Belt Conveyors are well-suited for transport tasks, such as indexing and positioning. Available with options for multiple lanes, they can be adjusted to handle various-size conveyed goods, such as the end-customer’s water bottles.
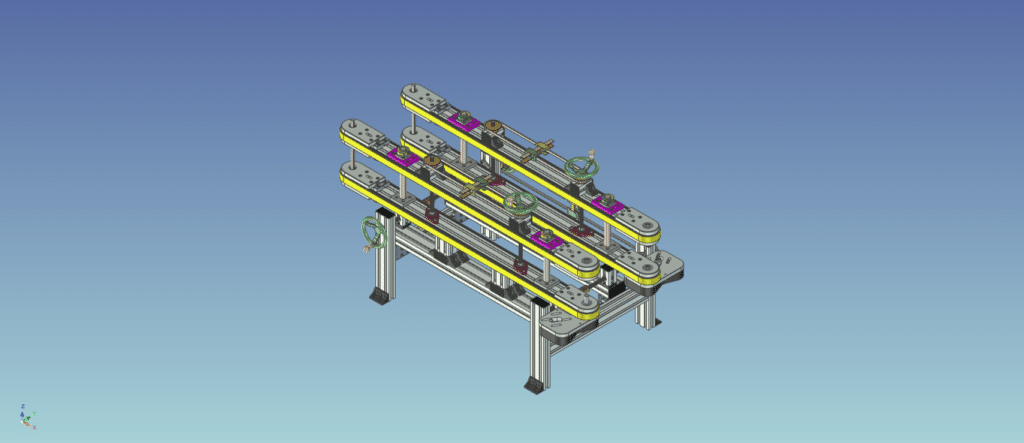
The customer chose Robotunits thanks to these readily available standard products. In addition, we also provided the framing for the conveyor system. Robotunits extrusions incorporate a unique 14-millimeter t-slot that makes them compatible with all other frames from our Modular Automation System.
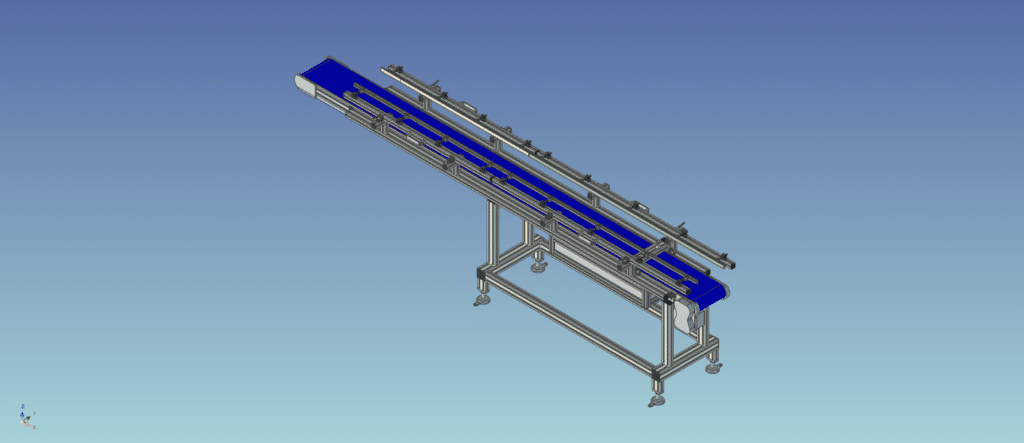
Here are some of the challenges the custom design presented, along with the approaches we took to solve them:
Space constraints. The preliminary design for the hugger conveyor section of the system called for a large frame to support the hugger conveyors. Due to space limitations, we explored a medium-size frame before opting for a four-legged frame with the hugger conveyors in the center of the assembly.
Smooth user adjustment. The customer specified two hand cranks so operators could raise or lower the conveyors, as well as adjust the conveyor widths to the corresponding bottle sizes. The components in the hand assemblies required excellent rigidity to ensure smooth motion. Our team responded with a 30-millimeter shaft that guides the Z-axis crank adjustability from the centerline, eliminating any binding and ensuring the conveyors remain straight during vertical motion.
Simplifying Challenging Automated System Designs
This successful application is an example of how our Modular Automation System products and customer support can make challenging conveyor projects simple to achieve. That’s because our highly standardized modular products are easily modifiable, and they can be implemented alongside existing equipment. In fact, our customer added its own components to the system without disassembly or removing parts.
Our engineers provided an effective system — built and tested in-house — and delivered it to our customer’s satisfaction. From quality engineering to collaborations that solve design challenges, we can help you create a complete automated production system.
For more information about our Timing Belt Conveyors, Linear Motion Units or Extrusion technology, please visit www.robotunits.com.